Advantage Book Binding is Looking for Skilled Machine Operators in Maryland
Advantage Book Binding is looking for skilled machine operators to work at its facility in Glen Burnie, Maryland. If you’re interested in joining our team as a skilled machine operator, please navigate over to our Careers page for more information. Please find the job requirements for skilled machine operators below.
Skilled Machine Operators
Position Responsibilities and Performance Indicators
“A” Operator:
This position reports directly to the shift Supervisor.
Definition:
An “A” Operator/Line Leader is a person who has been assigned to run a machine or an assembly line with 1 or more helpers to produce a given product. Such a person is given the authority by the supervisor to direct the helpers assigned to them and to critique their quality and performance.
Qualifications:
- The “A” Operator/Line Leader must be motivated, self supervised individual. They must be able to accept the authority given to them taking charge of the line they are overseeing. They must be able to communicate accurately and respectfully with fellow employees, temporary employees, and the shift supervisors.
- Knowledge – Demonstrate proficiency and/or familiarity with all equipment assigned to.
- Experience – No formal experience required although ability to run assigned machine/line is required.
- Skills/Aptitude – Ability to communicate necessary objectives, instructions to meet production requirements.
- Level – Works under minimum supervision, exercises moderate degree of discretion and independent judgment.
General Requirements:
Oversees manufacturing processes by directing all activities and crew within that process to achieve desired results consistent with company goals and quality requirements.
Primary Responsibilities and Indicators:
1. Safety
- Assures that all crew members are following safety procedures and awareness.
- Maintains a clean and safe work environment.
- Promotes a safe and clean work environment.
- Monitors equipment to assure all safety guards are in place.
2. Quality
- Monitors quality and assures work is produced to agreed standards.
- Performs QC pulls at defined timeframes and signs QC pull with name, quantity QC pulled, and date.
- Approves other production runs (OKs).
3. Variance
- Monitors and recommends staffing needs to optimize production rate.
4. Production/Scheduling
- Completes all documentation thoroughly and accurately.
- Determines the best technique that provides the best quality and best rate through communication with supervision.
- Reports production schedule variances to Supervisor.
- Submits production log to Supervisor at completion of operation.
5. Coaching, Leadership and Community Skills
- Assists Supervisor in evaluating employee performance.
- Promotes and is actively involved in continuous improvement.
- Recommends and manages change with a positive attitude.
- Fosters a TEAM environment.
- Trains others to assist in their personal growth.
- Communicates accurately and respectfully with others.
6. Other
- Promotes company policy and procedures.
- Performs Preventive Maintenance in accordance with PM schedule.
- Assists maintenance in the inventory of proper parts for equipment.
Direct reports: No formal direct reports. “A” Operator is responsible for managing their machine/line crew.
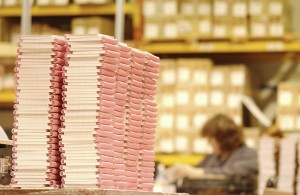